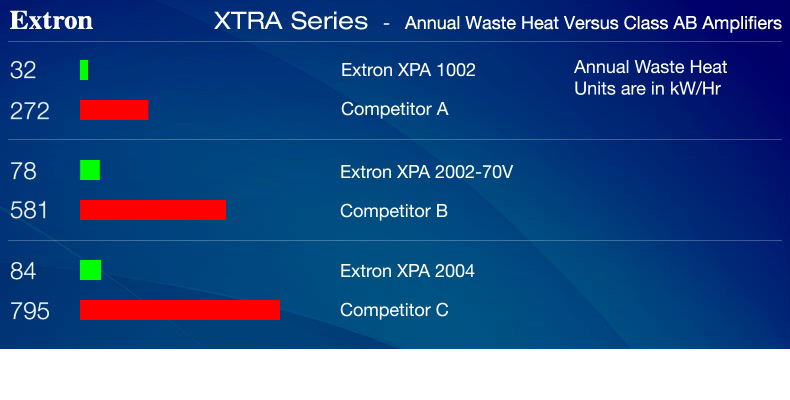
The Extron XTRA™ Series of Class D amplifiers are the commercial AV industry’s first complete family of ENERGY STAR® qualified amplifiers. These amplifiers are more energy efficient than conventional Class AB amplifiers, which means lower operating costs and less heat dissipation. Audio amplifiers are traditionally one of the biggest sources of energy consumption in an AV system.
Waste Heat
The energy efficiency of an amplifier is the ratio of audio output power to the input power drawn from the supply. The difference between the input power and the audio output power is waste heat, which must be dissipated. This waste heat can be expressed as watts or as BTU/hr - British Thermal Units per Hour. The relationship of watts to BTU is a straight conversion: 1 watt = 3.412 BTU/hr.
XTRA Series Amplifiers Generate Less Waste Heat
Table 1 shows waste heat calculations for the XTRA amplifiers versus conventional Class AB amplifiers. The numbers dramatically show that much more heat is being dissipated by the Class AB amplifiers. For example, Competitor B wastes 7.5 times more power than the Extron XPA 2002-70V. Equally dramatic differences can be seen for the other amplifiers.
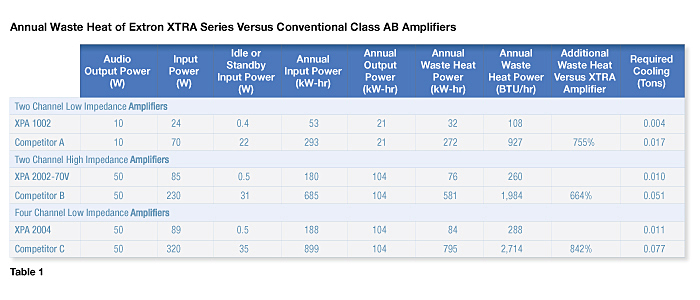
Managing Waste Heat in a Class AB Amplifier
Knowing now that Class AB amplifiers dissipate significant amounts of heat, the question arises, “How is this heat dealt with by the amplifier?” Thermodynamics dictates that heat will travel from a warm body to a cold body. Thermal energy dissipated from an amplifier’s circuit will travel to the cooler environment of the room or enclosure in which the amplifier is placed, such as a credenza or rack, until a state of thermal equilibrium is reached.
Products with components that generate more heat than can be maintained within a sealed enclosure, without thermally impacting the product, must be designed with measures to move out this dissipated heat. Open vents are an option to let the heat out, but it comes with the compromise of allowing foreign matter, such as salt air, dust, and other contaminants to enter the amplifier and compromise long-term performance.
Active cooling with fans is another option, but there are several compromises. The first is the issue of fan noise, which limits the possibilities for installation of a fan-cooled amplifier. Many meeting rooms have equipment racks or credenzas. Noisy amplifier fans can disturb these meeting spaces. The second compromise with fans is that they must be maintained as they can become clogged or closed with debris. If fans or their filter media become blocked, this prevents the passage of air necessary to cool the amplifier’s circuits, in turn causing performance issues or thermal shutdown. Third, the fan itself is a moving part, which limits the operational lifetime of the product.
When considering an amplifier for a system design, it is important to adhere closely to the manufacturer’s installation requirements. Some amplifiers require active cooling to maintain ideal operating conditions for the product. Others also require empty rack space above and below their product for thermal management. This will be explored further in the discussion on space efficiency.
The most important consideration with heat is that it shortens the lifespan of a product. Every 10° Celsius rise in temperature cuts the lifetime of the product in half. Heat dissipated from a thermally inefficient amplifier also shortens the life of other products mounted above it or nearby.
XTRA Series Amplifiers Run Cool for Increased Reliability
Extron has solved the potential problems resulting from heat dissipation by developing a thermally efficient Class D amplifier design that generates much less waste heat. XTRA Series amplifiers have an extremely low operating temperature that does not require fans or vents. They are convection cooled with a sealed enclosure that prevents incursion into the amplifier by foreign material.
This translates to a very long operating lifespan for the XTRA Series. Full rack-width amplifier models such as the XPA 2002 and XPA 2004 are rated for 200,000 hours MTBF - Mean Time Between Failures, while the half rack-width XPA 1002 and XPA 2001 amplifiers are rated for 250,000 hours MTBF. The low-heat signature is a key component in the long-term reliability and longevity of XTRA Series amplifiers.
A dramatic comparison of the heat dissipated from a conventional Class AB and an XTRA Series amplifier is shown in Figure 1. Under 1/8th power conditions, the hottest point on the Class AB amplifier measured 74° C (165° F), while the hottest point on the XTRA Class D amplifier was just 38° C (100° F).
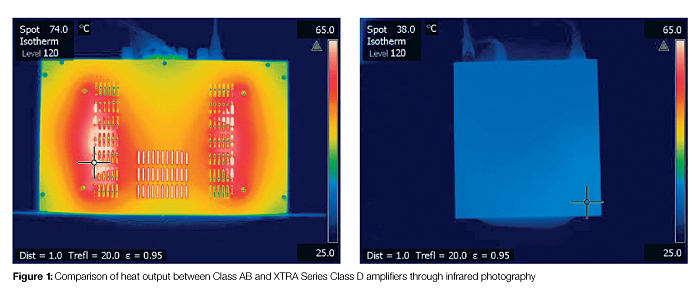
Where Does the Dissipated Heat Go?
Heat dissipation must be factored into the system design. Less thermally efficient products add expense to the bottom line in terms of infrastructure costs and operational costs.
An enclosed space could be an equipment rack in an AV equipment room or lectern, custom millwork–a term for custom cabinetry in a meeting room, or meeting room casework–sometimes referred to as credenzas. Some of these locations, such as equipment racks, are intended for AV equipment and have proper venting and forced-air cooling. In the case of podiums, millwork, and casework, equipment heat loads must be carefully considered with respect to heat management. Heat loads out of balance with the immediate ambient environment will cause products to overheat, compromising their performance and possibly leading to shutdown. The end result is a system offline, costing productivity hours and requiring a system redesign.
XTRA Series Amplifiers Minimize Thermal Impact in Small AV Systems
The relative thermal impact of an XTRA Series Class D amplifier can be illustrated for a small AV system. Table 2 shows a list of AV products for a small AV system with their measured power and heat dissipation. This system includes a control processor, twisted pair receiver, an HD tuner, audio matrix processor, presentation switcher, Blu-ray Disc player, and a desktop PC. Also included is the Class AB amplifier from Competitor A.
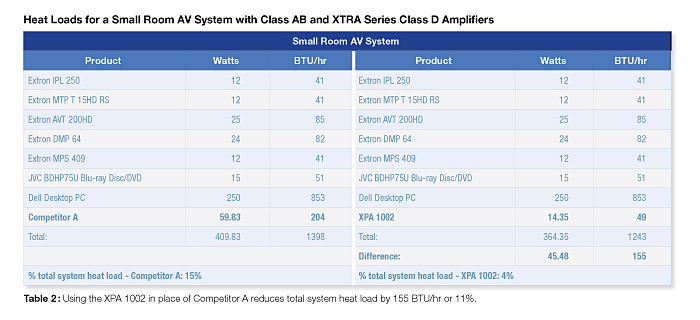
The data for Table 2 was generated following a standard industry practice of calculating waste heat from the AV equipment, by totaling each product’s published or calculated wattage, and multiplying that figure by 3.412 to get BTU/hr. If a product uses an external power supply, the wattage of the power supply is used as a worst case scenario to create a cushion in the heat load figures. If amperes were provided in a manufacturer’s specification in place of watts, that figure was converted to watts using Ohm’s law and the published voltage. For example, 1 amp x 12 volts = 12 watts.
With the Class AB amplifier, the system has a total heat load of 1,398 BTU/hr, whereas with the Extron XTRA Class D amplifier, the system heat load is 1,243 BTU/hr. The Class AB amplifier represents 15% of the total heat load of the system. The heat load must be managed with proper ventilation of the rack, millwork, casework, or podium. The more confined the space, the more critical proper ventilation is to the system design. Costs are incurred if a cooling solution must be added to any of these enclosures.
When the Extron XPA 1002, at 49 BTU/hr, is exchanged for Competitor A at 204 BTU/hr, the XPA 1002 will contribute just 4% of the total system heat load, and subsequently reduce heat load by 11% in comparison to Competitor A. The reduced heat dissipation may be enough to avoid the need for forced-air cooling in the enclosure.
XTRA Series Amplifiers Can Reduce Cooling Costs for Large AV Systems
For larger amplifier systems in which several units are placed into an equipment rack, not only must the enclosure venting be considered, but also the cooling of the equipment room into which the system is placed. The more amplifiers added to the system, the more heat is dissipated into the room and therefore, the more cooling required to maintain an ideal operating temperature. Energy efficient Extron Class D amplifiers will significantly help reduce facility infrastructure costs as well as annual operating costs.
If the temperature in the equipment room is not properly maintained for the heat load, then cool air cannot replace the warm air in the rack, preventing proper convection to adequately cool the system. Rack equipment manufacturers offer nomographs and white papers that can help determine proper rack cooling strategies. Whether the equipment rack is to be passively or actively cooled will depend on the equipment and heat load.
The HVAC - Heating/Ventilation/Air Conditioning industry measures air conditioning systems in tons, in reference to the cooling capacity of melting a 2,000 pound block of ice per hour. This capacity can be translated to BTU/hr with a straight calculation of 1 ton of cooling equaling 12,000 BTU/hr. Therefore, for every 12,000 BTU/hr of system heat load, one ton of air conditioning will be required.
XTRA Series Class D Amplifiers
Extron XTRA Series amplifiers deliver a combination of energy efficiency, low heat dissipation, and space efficiency that lowers ownership costs for facilities compared to installing conventional Class AB amplifiers. For more information, download the XTRA Series efficiency white paper at www.extron.com/xtrapaper.